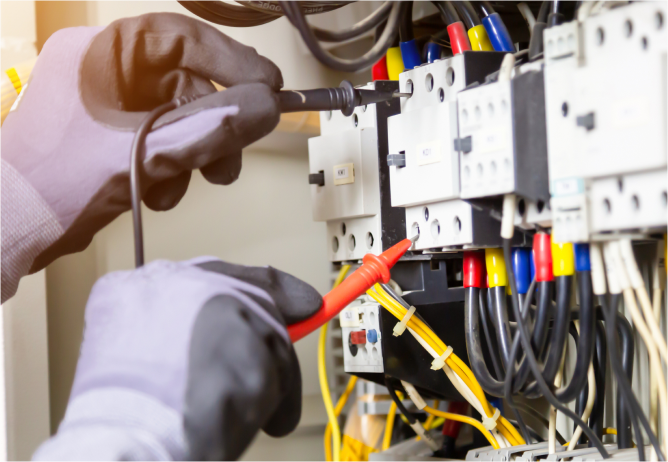
Customised Solutions Utilising Leading-Edge Technology
At Hamilton Research we work closely with customers to create innovative solutions that transform ‘black-box’ control systems into ‘open-box’ systems by customising the control system to their specific requirements. In the past, Hamilton Research has enabled customers to exceed the global average of current efficiency (94%) thereby increasing the customer’s productivity and consequently their profitability.
We enhance the life of the system thereby reducing the customer’s maintenance costs and improving the bottom line with our reliable and robust electronic modules. Most electronic modules have an MTBF of over 10 years of continuous operation and MTTR of less than 30 minutes. We strive to enhance operational efficiency and effectiveness for each aluminium plant and help them avoid unnecessary infrastructure upgrades.
Dedicated Customer Service and Technical Support
Hamilton Research has provided electronic replacement modules for the original system not offered by OEMs. We have customised over 30 such electronic modules.
We have become a trusted partner of –
- Renukoot (1990)
- Hirakud (2000)
- Vedanta (2006)
providing on-demand troubleshooting and solutions so there is no interruption in the production process.
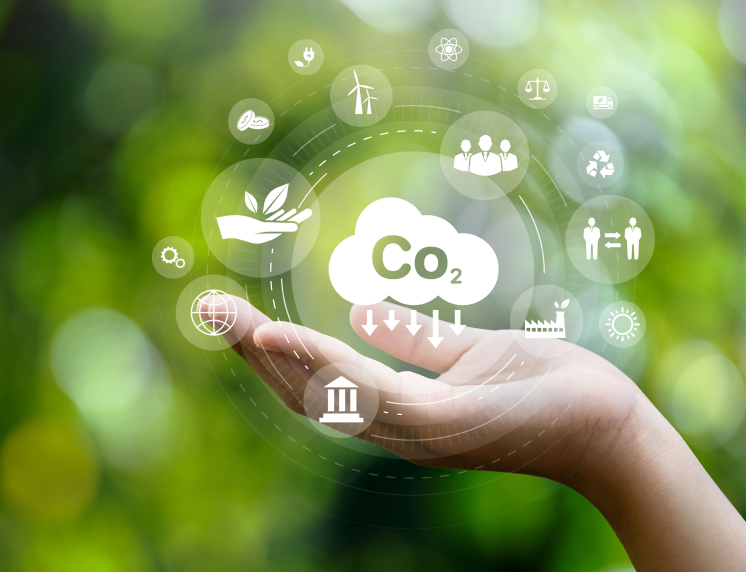
Aligns Customer’s Business Goals with Environmental Responsibility
Hamilton Research is committed to enhancing the production process in aluminium smelting plants with environmentally responsible solutions. We have successfully brought down average power consumption to 13,000-13,150 units for every ton of aluminium produced.
Additionally, we have achieved a significant reduction in greenhouse gases (GHGs) generated during aluminium smelting. With world-class technical parameters, our systems bring the Anode Effect Frequency in the range of 0.06 to 0.2 with anode effect duration of about a minute. Our solutions enhance production, lower outlays and help clients make sustainability a priority.